Swedish steel prize winner 2013
Mack Trucks Inc
2013 | Mack Trucks Inc. - part of Volvo Group | USA Winner 6 min read
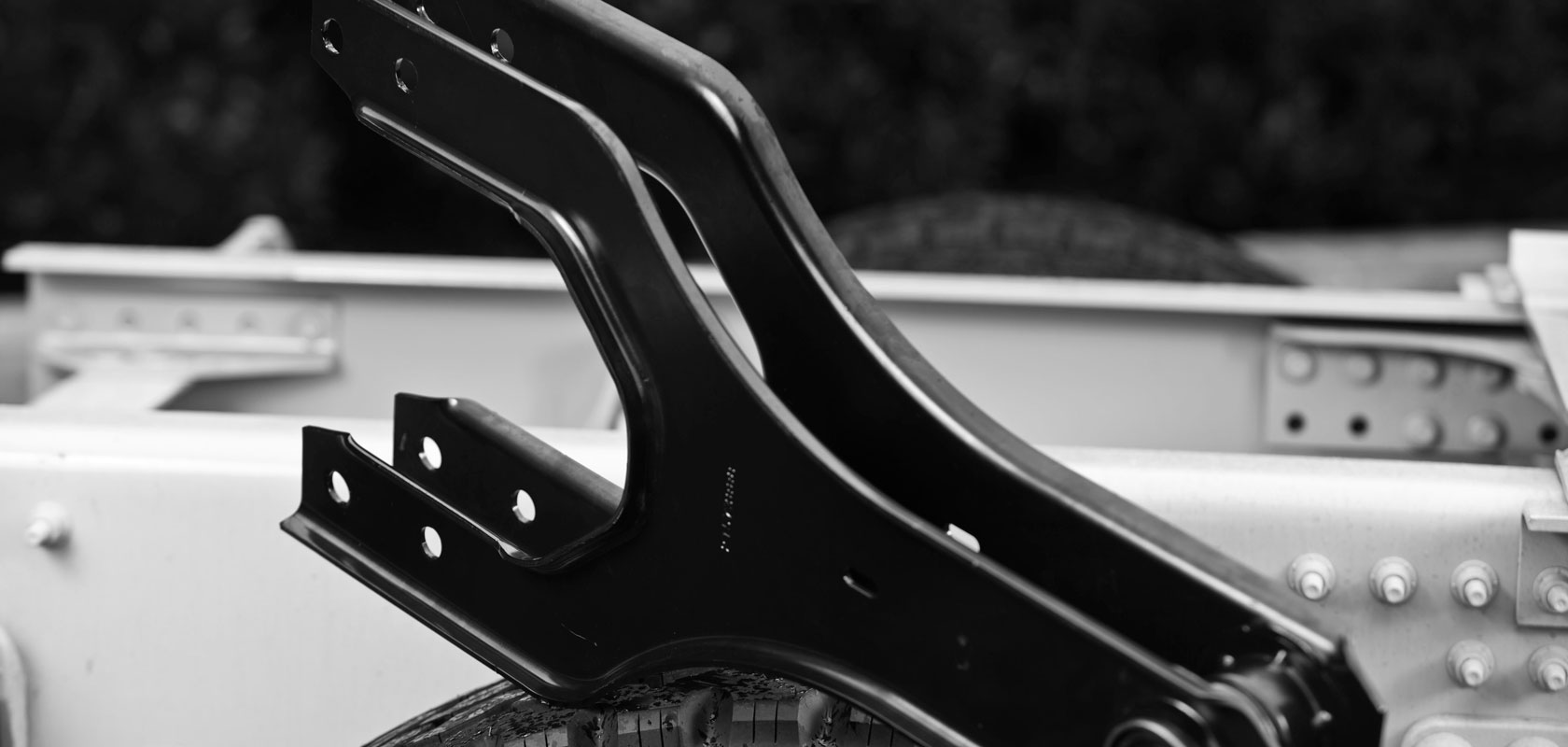
The Twin Y is an entirely new principle for truck suspensions which is not only lighter, but offers considerably improved handling. The design is based on a supporting arm comprising two interlocking sections made of high-strength steel, which absorb the forces exerted upon the vehicle’s rear axles in an entirely revolutionary way. This new solution reduces vibration and increases tire traction. Not only are steering, braking ability and driver comfort considerably improved, but Twin Y also significantly reduces tire wear. Similarly, Twin Y is also lightweight and sturdy, meaning that the suspension has a long serviceable life and low maintenance costs.
Mack Trucks has introduced the new suspension on the rear axles of its highway transportation trucks. They have been fitted to the Mack Pinnacle since early 2013 - a truck model designed for hauling heavy loads over long transcontinental routes in North America.
Twin Y consists of two stamped steel blades made of Domex 100 XF/Domex 700, which absorb the vertical movements of the axle through the air suspension component of the suspension system.
Twin Y benefits from both the strength and flexibility of high-strength steel and represents a revolutionary way to counteract the motion generated by the axles.
This improves road handling, which in turn results in a considerable reduction in tire wear - one of the three major expenses for a hauler. A longer serviceable life also means fewer maintenance stops for tire changes and rotations or for maintenance on the suspension itself.
The new design can save up to 180 kg (400 lbs) in weight per truck compared with other air suspension systems.
The high-strength steel design also results in a significantly simpler, cleaner and more efficient manufacturing process for Mack Trucks.
An in-depth look
A: DESIGN AND TECHNOLOGY
The key component of the new Twin Y suspension is a supporting arm with two mirrored, Y-shaped sections of 5mm Domex 100 XF/Domex 700. Equally important to the function of the Y-shape is the fact that there are just two blades in a twin set. The supporting arm is positioned in front of the axle. Behind the axle are a standard air suspension and a shock absorber.Both arms of the Y-section are fixed to the top and bottom of the axle house, providing a direct and stable grip on the axle. The two sections together provide a double grip, whereas traditional suspension systems are fixed only to one side of the axle.
“It’s like grabbing something with two hands instead of one,” explains Greg Kiselis, the Principal Engineer who thought up the idea and developed the concept together with the design team.
When subjected to compressive forces, the supporting arm is completely rigid not only vertically but also horizontally, thanks to a folded C-shaped section around the entire structure. As the Twin Y hangs down from a bracket in front of the axle, you could say that it pulls its load behind it. All of the vertical force is then transferred to the air suspension at the rear of the axle. The advanced axle attachment reduces direct compression stresses on the suspension and thereby contributes to improved traction and braking ability. But the design is vitally important for other reasons.
Laterally, the Twin Y works flexibly and therefore allows the lateral torque rod to take all of the lateral force.The spring-like characteristics of the high-strength steel work together with the geometry of the double sections. Twin Y is joined using screw joint reinforcements with welded casing at five points - four on the attachment to the axle, and one where the supporting arm is fixed to the chassis.
When you see the Twin Y sit between the longitudinal beams and axles, you are struck by how slim it is compared to other parts of the rear axle. Both Y blades weigh just 22.5 lbs, a little less than 10 kg.
“The whole idea is based on the use of high-strength steel. The blades must be thin, flexible and strong. The design wouldn’t work if we had been forced to use thicker materials to get it to hold. The outcome would be that the blades would start to take load laterally,” Greg Kiselis explains.
The earlier design required hard and rigid steel, which ultimately results in fatigue. “If you want a suspension member that acts like a spring to last longer, you have to make it softer,” Greg says.
“We’ve chosen strong and flexible steel and stamped it into a shape which provides rigidity in the directions where it’s needed. Laterally we use Domex’s spring-like characteristics.”
Thanks to the design, a softer rubber can be used for all of Twin Y’s bushings to further reduce vibration. Similarly, the attachment of the supporting arm to the truck chassis is not subject to any significant forces laterally.
“We can use extremely narrow tolerances for holes and casings. Compared to the previous design, the rubber of the bushings is three times softer, which enhances comfort even further,” Greg Kiselis explains.
Normally, all of the bolts in a suspension system are tightened after a certain number of kilometer, but since Twin Y reduces vibration, there does not tend to be any loosening. To further ensure that trucks fitted with Twin Y don’t require re-torqueing at the service center, Huck U-bolts are used that lock in place.
B: THE BENEFITS OF TWIN Y SUSPENSION
For the customer, Twin Y has a number of benefits:
Less vibration has a chain of positive effects:
- Improved tire traction to improve steering and reduce tire wear.
- Less vibration in the cab to improve the driver’s working environment.
- Tire traction helps to reduce fuel consumption.
- Less vibration in combination with the high-strength steel design results in a longer serviceable life and lower maintenance costs.
- Twin Y weighs 400 lbs/180 kg less than comparable air suspension systems. Less torque reactivity means fewer vibrations in the driveline system.
Twin Y offers Mack Trucks a simple and clean manufacturing process. The holes are laser-cut and the sections stamped, while no post-processing is required after welding.
The previous design required a tedious and dirty curing process.
“The press punches out a new blade every six seconds. We’ve gone straight from working with a blacksmith technique to a technology that belongs in the 21st century,” Greg explains.
Jerry C. Warmkessel, Marketing Product Manager at Mack Trucks, has worked for the company for over 40 years, and concludes:
“This is the biggest thing I’ve seen in all my years in the truck industry. Twin Y represents a dramatic improvement.”
C: DEVELOPMENT WORK
Greensboro, North Carolina.
Greg Kiselis remembers exactly when he presented his idea to Michael A. Brown, Director for Product Management. It was Aug. 10, 2007. At that time, Greg had been working in the automotive industry for almost 20 years developing and refining suspension systems. His old manager, Michael, had lured him over to the truck industry.
Greg quickly noticed that there was a lot to be gained from a revolutionary new high-strength steel design. There was no question of using Domex to build Twin Y. He finds it difficult to hide his pleasure with the material’s consistent characteristics and good formability.
From the perspective of cars, traction is a characteristic feature of premium vehicles. The car glides over the road ahead while the suspension handles all the road’s imperfections with no effect on those sitting within.
“A truck is a completely different story. But with my background, I was surprised that no one had made a proper attempt to enhance comfort for truck drivers.
I’m glad I had the opportunity to take on the challenge,” Kiselis said.
The Twin Y design is replacing a component called a Z-spring. This is essentially a traditional leaf spring combined with air suspension. When air suspension systems came in, one half of the leaf spring pack was essentially cut away. The leaf spring’s front joint to the frame was retained, and the cut end was attached to the axle. This is a common solution found in numerous variants on most of these types of trucks in the North American market.
The principle of a Y-shaped single blade already existed when the project began, one of the unique concepts of the suspension was to use two blades. The idea was then developed using advanced calculations and 3D simulations.
Development work took place in Greensboro, North Carolina where Mack Trucks’ headquarters are based and where it shares a huge test track with parent company, the Volvo Group. Test drives subject the vehicle to extreme conditions – uneven stone surfaces, deep potholes, incorrectly sloped G-curves and concrete formations which force the axles to make powerful counteractive movements.
The first tests using Twin Y began in 2009, and Greg has now spent hundreds of hours together with test drivers. One vehicle fitted with Twin Y has been driven for over 450 test cycles (normal test is 300 test cycles).
“We realized early on that the tires were lasting many more laps than is usual during testing. It was not unexpected in itself, but this performance was surprisingly good,” says Greg Kiselis.
Before Twin Y was launched to the market in January 2013, a number of customers were able to conduct long-term in-service testing.
“All of those who tested the system were very satisfied with the steering, and especially the cornering ability. The wheels show no tendency of swinging back.”
The highway transportation trucks now equipped with Twin Y travel enormous distances, often non-stop on the transcontinental coast-to-coast routes of the U.S. and Canada.
“We get a lot of comments about how much better the tracking of the trucks is, as well as how comfortable the trucks are with the Twin Y suspension. One of the drivers said that he can now sleep well in the cab while his colleague is driving. When you include all the other benefits such as reduced tire wear and how lightweight the Twin Y is, it becomes clear that Twin Y makes a win-win solution,” says Greg Kiselis.
D: MACK TRUCKS, PART OF VOLVO GROUP
Mack Trucks, part of Volvo Group, is one of North America’s largest producers of heavy-duty trucks. MACK® trucks are sold in more than 45 countries. Mack trucks and diesel engines sold in North America are assembled in the United States.
The corporate symbol is a bulldog, which adorns the radiator of every Mack truck. Many of the company’s trucks are classics of American trucking culture, such as the B series from the 1950s.
The U.S. market for heavy goods vehicles is much associated with traditional thinking, but today’s customers demand lower weight, fuel efficiency and advanced driver assistance.
“The fact that we are now designing our cabs for all types of drivers is typical of this. We are living up to the needs of a global market in which customers have a variety of different needs,” says Jerry C. Warmkessel, Marketing Product Manager at Mack Trucks.